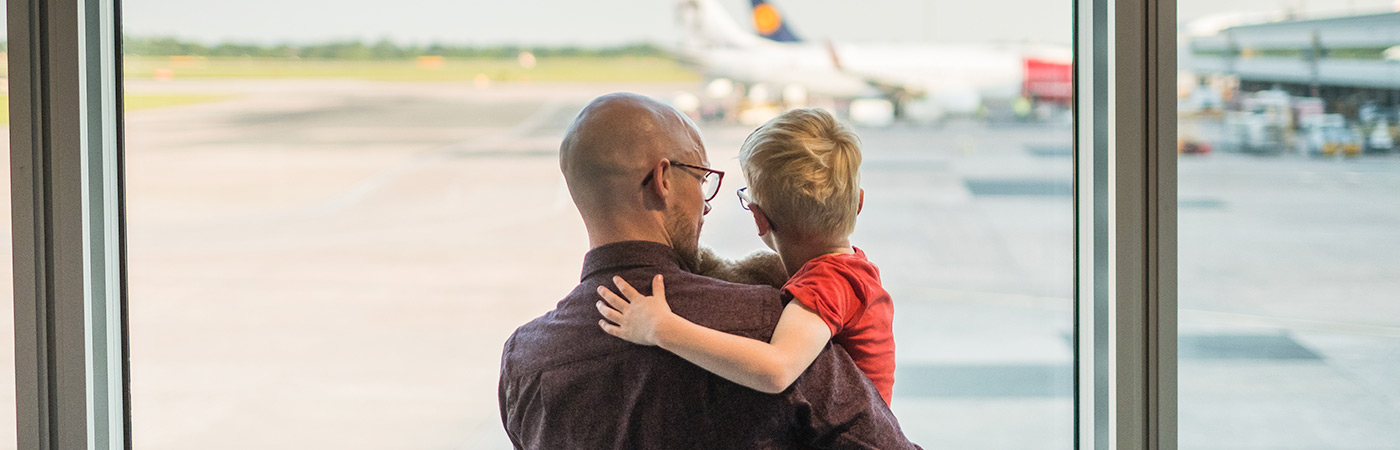
Setting global standards – making aero engines perform even better
Air travel is taking us further, more quickly, more often. Meeting this growing demand requires evermore rigorous standards of safety. Setting global standards in this area, Rolls-Royce worked with world-leading materials scientists at The University of Manchester to help produce engines that deliver optimum performance and safety standards.
Global problem: tiny cracks that could be a big issue
Research beacon breakthroughs
Find out how world-class academic research is commercialised by scientists, engineers, medical professionals, business leaders and policymakers at Manchester.
Fan blades in aircraft engines endure large loads and high-frequency vibrations. Over time, these stresses can create microscopic cracks in the blades which can lead to issues in service.
The traditional method for stopping cracks is ‘shot-peening’, ie firing shot (round metallic, glass or ceramic particles) at the blades in order to rework the metal’s surface. The shallow indentations create compressive residual stresses that stop cracks growing.
Rolls-Royce wanted to explore alternative cutting-edge methods with leading experts at Manchester. The academic task force therefore investigated laser shock peening (LSP), which introduces compressive stresses to a much greater depth via plasma created by a powerful pulsed laser.
Manchester solution: stress management for stronger materials
Manchester researchers worked with Rolls-Royce to study the fundamental nature of LSP-induced compressive residual stress. LSP has demonstrated it is an improvement on more established shallow peening: it effectively compresses the atomic structure of the fan blades to make them much more resilient to cracking and fatigue.
"The combination of academic leadership, relevant research expertise and our ability to work closely with industrial partners makes Manchester stand out in this field. Rolls-Royce trusted our evidence and immediately adopted LSP to treat its Trent 800 engines.”
Philip Withers / Regius Professor of Materials
Professor Philip Withers, Regius Professor of Materials, received the Armourers and Brasiers’ Company Prize from The Royal Society in 2010 in recognition of his use of neutron and hard X-ray beams to map stresses and image defects.
He says: “Our team analysed the potential of LSP to improve fan blades' fatigue resistance by using penetrating synchrotron X-ray beams.
"We discovered that this method generates deep compressive stresses which remain stable during air travel. This testing confirmed LSP could be safely applied to the fan blades to make them stronger and last longer.
"We’ve got excellent facilities and expertise at the Materials Performance Centre, Engineering and Process Metallurgy Group, and Materials Testing and Analysis Unit.
"The combination of academic leadership, relevant research expertise and our ability to work closely with industrial partners makes Manchester stand out in this field.
"Rolls-Royce trusted our evidence and immediately adopted LSP to treat its Trent 800 engines."
Industry-changing impacts
The University’s research into LSP for Rolls-Royce has led to:
- LSP being used to treat all Trent 500, Trent 800, Trent 100 and XWB blades, making millions of air travellers safer every year;
- a longer lifetime for a high-investment product – sales of 1,200 treated Trent XWB engines alone are worth more than £60 billion.
Find out more
Read the research papers:
- 'Effects of fatigue and fretting on residual stresses introduced by laser shock peening', Materials Science and Engineering, Vol 435-436, 2006
- 'Engineering the residual stress state and microstructure of stainless steel with mechanical surface treatments', Applied Physics, Vol 99, Issue 3, 2010
Meet the researchers:
- Professor Philip Withers, Regius Professor of Materials
- Professor Michael Preuss, Professor of Metallurgy
- Dr Philipp Frankel, Research Fellow
- Professor Dave Rugg, Corporate Titanium Specialist, Rolls-Royce plc